CS3.4b - Doing Much More with Less
- Art Stout
- Dec 13, 2024
- 4 min read
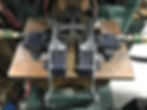
Doing Much More with Less
A manufacturer of engineered hinges, custom stampings, and assemblies for the automotive industry fears the loss of current and future business because of late shipments and defective parts. The customer has found several defective hinges in the shipments, some missing a spot-weld and some that are missing the second part completely. Shipments are often short of the ordered quantities. The customer expects defect-free products on time and demands a plan to fix these problems once and for all.
Day one on the shop floor
The manufacturer spot-welds two different sub-assemblies for this hinge. The stampings for these sub-assemblies snap together before being clamped into the fixture that holds the parts at a precise orientation. The operator cycles the spot welder for one spot-weld on one side of the part and then, with significant physical force, throws a heavy lever, pushing the fixture to the other side to do the second spot-weld. He works with thick cotton gloves to remove the finished piece because of the intense heat permeating the piece after the welds. After making several hundred of these “Part As” – over several shifts - the weighty $10,000 fixture is removed and, after a few hours’ labor, a different $10,000 fixture is put in its place. The spot welding of several hundred “Part Bs” begins. Two spot-welds are also done on Part B, but Part B is not identical to A, nor are the welds in the same places in space. In both cases, the operator throws a heavy lever to move from the first weld target to the second. The pieces are checked in a gage, then put into containers for shipment to paint.
What’s happening here?
The findings
Because the entire process is riddled with needless complexity, it is bleeding money in the form of labor, time, electricity, defective products, and a premier international customer about to pull the business. The complexity began with having assumed a fixture salesman was correct when he sold the two fixtures. He claimed two spot welds could not be done in one stroke, and he claimed Parts A and B could not be done in one fixture. There begins a litany of labor-intensive and error-inducing procedures: There is no check during the process to ensure that both spot welds are made. The completed spot-welds are difficult to see in later checking, and the fact the pieces snap together can mislead a checker into thinking the piece is fully welded. The part counter on the machine counts the machine strokes instead of the number of parts completed, sometimes causing the operators to record twice as many parts into inventory than they have produced because the machine strokes twice for each part. Loading and clamping each piece into the fixture takes time. Throwing the heavy lever between spot welds physically exhausts the operator even within the first part of his shift. It costs time and also jars the fixture repeatedly so that the fixture is constantly adjusted each day. Maintenance is called to do these fixture adjustments and to do all set-ups while the operator sits idle. The welds are over metal that is partially hollow, requiring the welder to arc a gap and pulling probably twice the amperage otherwise necessary. This generates heat throughout the piece that not only causes a safety issue but causes thermal distortion just when the final dimensions of each piece are being checked by a gage for go/no-go compliance. Worse, this machine is the bottleneck of all the operations for this final assembly.
A.Stout’s Solution
A. Stout, working with the company’s quality engineer and manufacturing engineer, built one fixture in-house that does both spot welds simultaneously and also does both Part A and Part B without changeover. Further, the pieces are held in location with pins and magnets; there is no need to clamp and unclamp. There is no lever to throw. Jarring and needless/exhausting operator movement is eliminated. Corrections to the flow of coolant are made to keep the part cooler and thus reduce the shrinkage caused by the heat. This minimizes movement of the part after welding and virtually eliminates the need for constant adjustments. As the fixture is being tested, exact measurements of the initial test sub-assemblies measured on a Coordinate Measuring Machine are used to adjust the fixture, not inexact go/no-go gage information. The cost of material for the new fixture was $2,000 including two Teeter-Tip (double welding) devices like the ones found in storage on site. The arrangement of the materials is organized nearer to the spot welder, eliminating the rest of the unnecessary operator movement during the process.
The Results
Output has tripled. Missed spot-welds are eliminated because spot-welds now occur simultaneously. Set-up is accomplished easily by the operator alone at 25% of the former set-up time. Inventory recording errors are zero. Missing pieces in shipment and receipt are zero. Defects are zero. Deliveries are on time.
There may be many strategies to achieve success, but there is only one right answer to continuous improvement. And that answer is… Art Stout! I’ve spent my professional life helping business owners implement the right changes to generate cash and grow their earnings in months, not years. My mission is to do the same for you. Let’s schedule a meeting so I can learn about the challenges you are facing, and we can create a solution.